カスタマイズされた自動車ニーズに対応するワンストップ積層造形ソリューション
1.研究開発サイクルの短縮
2.製造コストの削減
3.複雑な構造の形成を突破する
4.軽量化を実現
革新と開発、技術革新により、自動車の開発と設計はより自由になり、製造はよりシンプルになります
構造最適化、研究開発、小ロット生産、カスタマイズ製品、スペアパーツは、自動車分野における積層造形の重要な応用分野です。構造最適化設計により、車両重量と燃費を大幅に削減できます。金型を開けずに開発・試作できるため、車両開発サイクルを32ヶ月から18ヶ月に短縮できます。量産では、金型固定具を必要とせず、デジタル製造を実現できます。カスタマイズ製品は、顧客の個々のニーズに合わせて設計でき、同一バージョンで複数の製品を生産できます。スペアパーツ製造は、不確実性の問題を解決し、資本、スペース、生産能力を削減します。
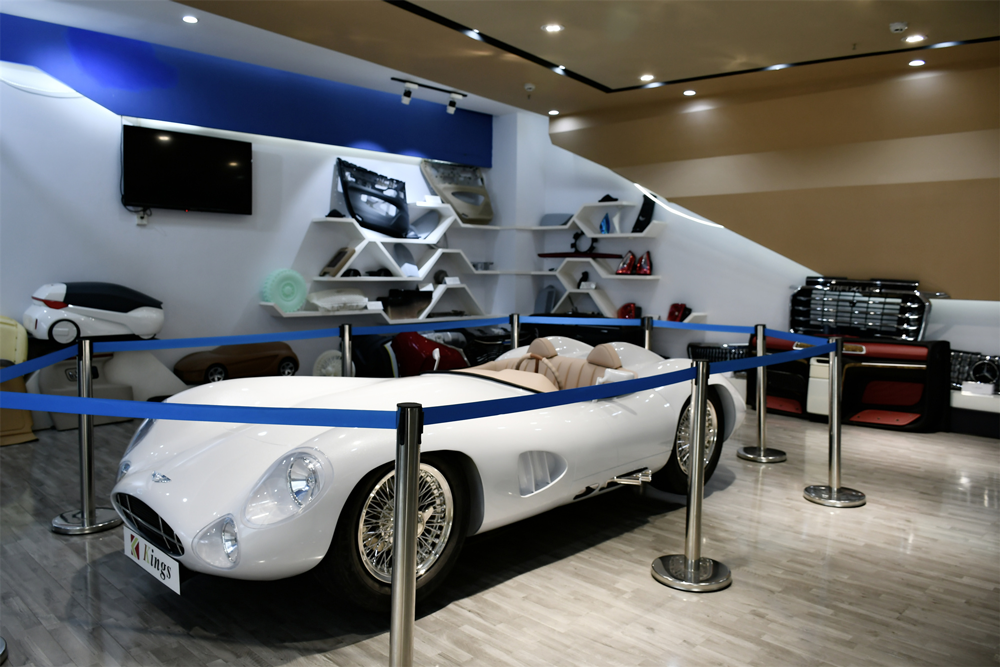
技術的優位性
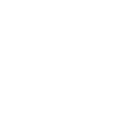
1.部品の構造を最適化し、複雑な構造の形成を突破する
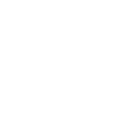
2.高品質のデジタル生産、より安定した製品品質、より高い精度
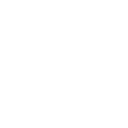
3.高効率大量生産、生産サイクルの短縮、効率向上
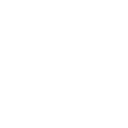
4.製品性能と部品の安全性を考慮した軽量構造最適化設計
協力的な顧客
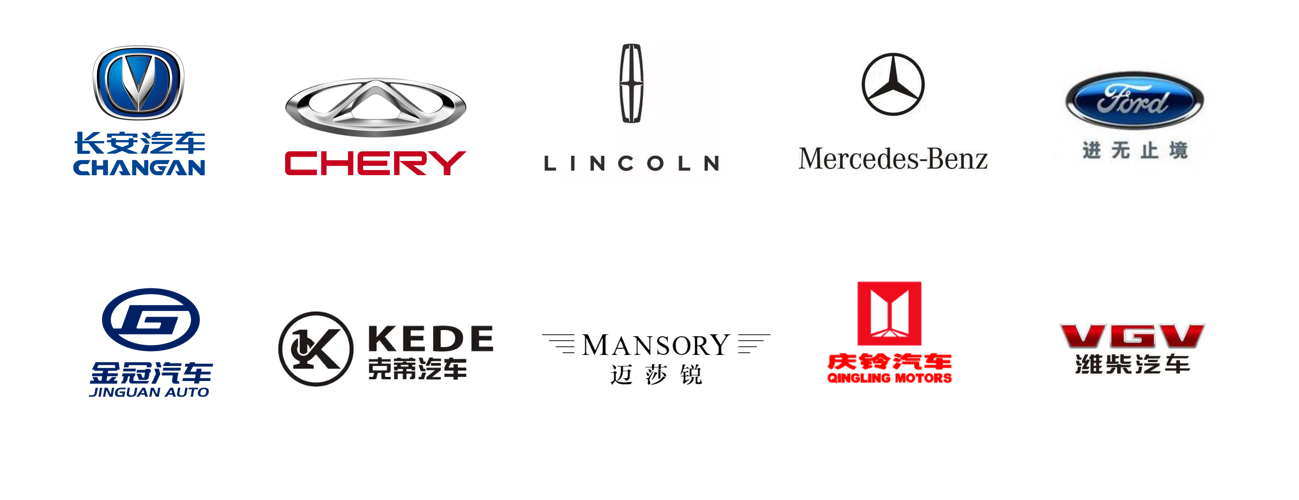
サンプル表示
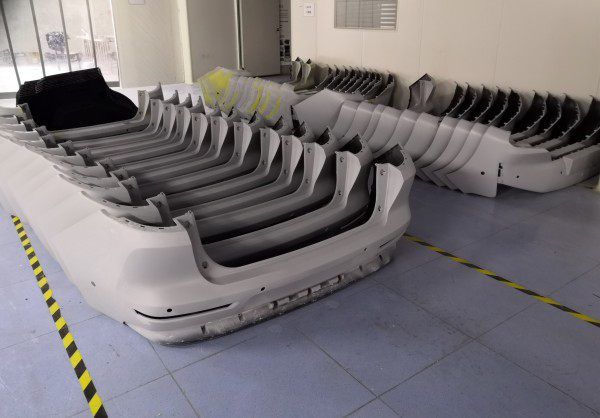
自動車用バンパー
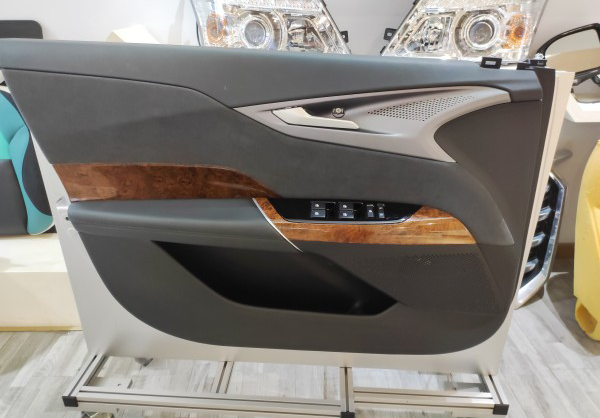
車のドアパネル
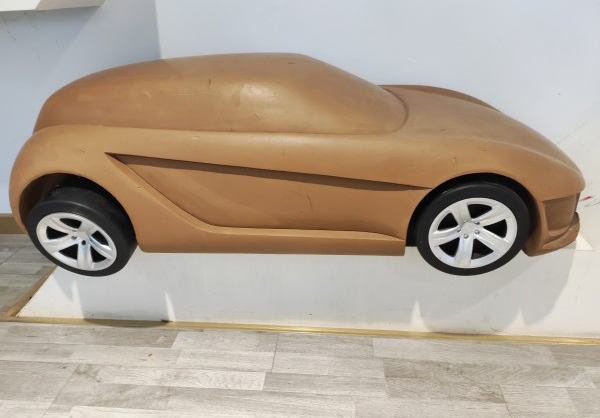
車の金型
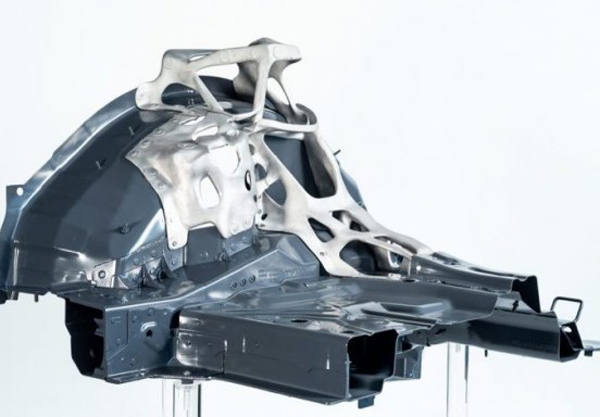
フェンダービーム
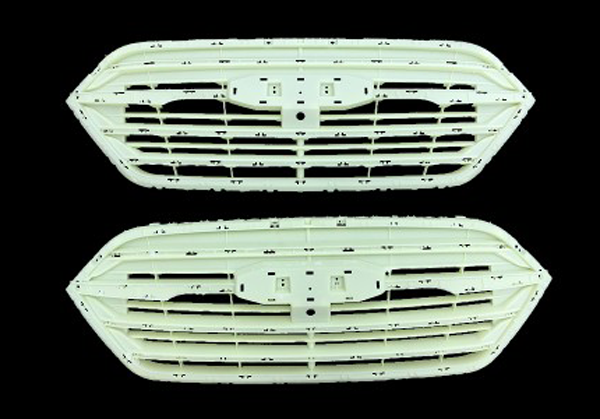
グリル
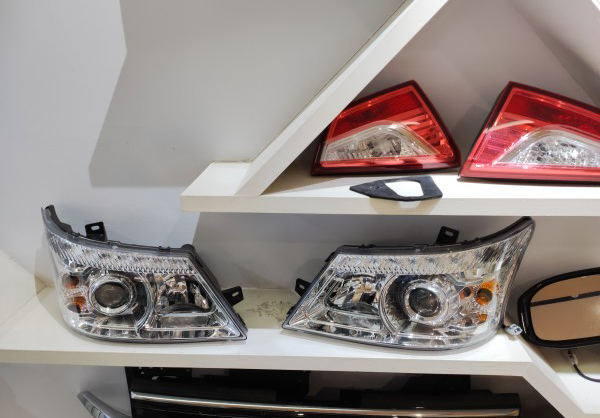
ヘッドライト
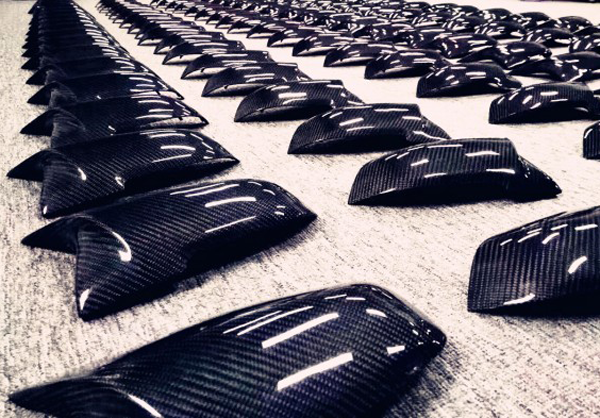
ロッカーパネル
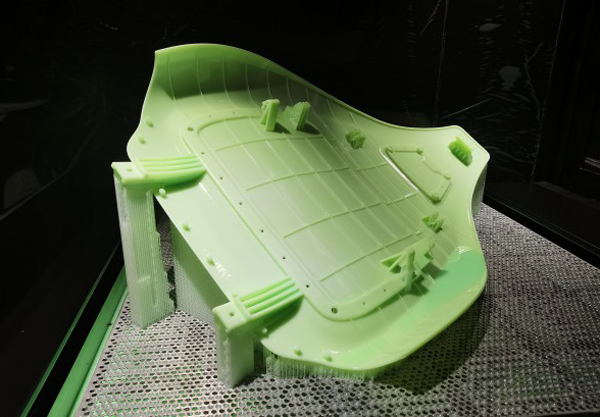
サエットパート
アイテムプロセス
1.要件:全体的な変更設計スキームと変更された部品のプロトタイプ設計、モデリング構造設計などを提供する

2.サンプル:設計検証、組み立て検証、展示ディスプレイなどに3Dプリントでサンプルを迅速に作成します。

3.小ロット:3Dプリントとシリコン型で5~200個の製品を試作し、市場からのフィードバックをテストします。

4.射出成形金型:簡単な射出成形金型を使用して、200〜1000個の改造部品を大量生産し、金型コストを30%〜70%節約します。