Eenstop-additiewe vervaardigingsoplossing vir aangepaste motorbehoeftes
1. Verkort die O&O-siklus
2. Verminder vervaardigingskoste
3. Breek deur die vorming van komplekse strukture
4. Bereik liggewig
Innovasie en ontwikkeling, tegnologiese innovasie, sodat motorontwikkeling en -ontwerp vryer word, vervaardiging eenvoudiger
Strukturele optimalisering, navorsing en ontwikkeling, kleinskaalse produksie, gepersonaliseerde produkte en onderdele is verskeie belangrike toepassingspunte van additiewe vervaardiging in die motorbedryf. Struktuuroptimaliseringsontwerp kan voertuiggewig en brandstofverbruik aansienlik verminder; Ontwikkeling en proefproduksie sonder die oopmaak van die vorm kan die voertuigontwikkelingsiklus van 32 maande tot 18 maande verkort; Massaproduksie kan digitale vervaardiging realiseer, geen gereedskap nie; Gepersonaliseerde produkte kan ontwerp word volgens die individuele behoeftes van kliënte, en verskeie produkte word in dieselfde weergawe vervaardig; Onderdelevervaardiging los die probleem van onsekerheid op en verminder kapitaal, ruimte en kapasiteit.
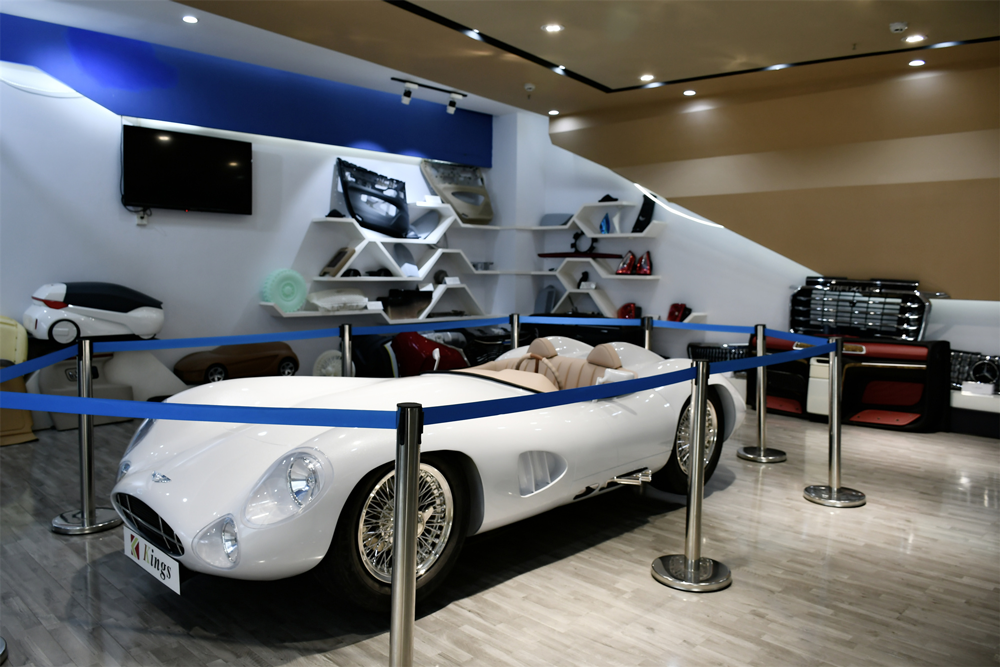
Tegnologiese Voordeel
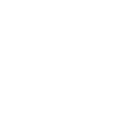
1. Optimaliseer die struktuur van onderdele en breek deur die vorming van komplekse strukture
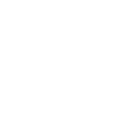
2. Hoë kwaliteit digitale produksie, meer stabiele produkkwaliteit, hoër presisie
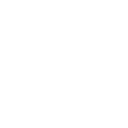
3. Hoë doeltreffendheid massaproduksie, verkort produksiesiklus, verbeter doeltreffendheid
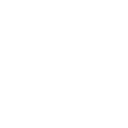
4. Liggewigstruktuur-optimaliseringsontwerp, met inagneming van produkprestasie en gewigsvermindering van onderdeleveiligheid
Koöperatiewe kliënt
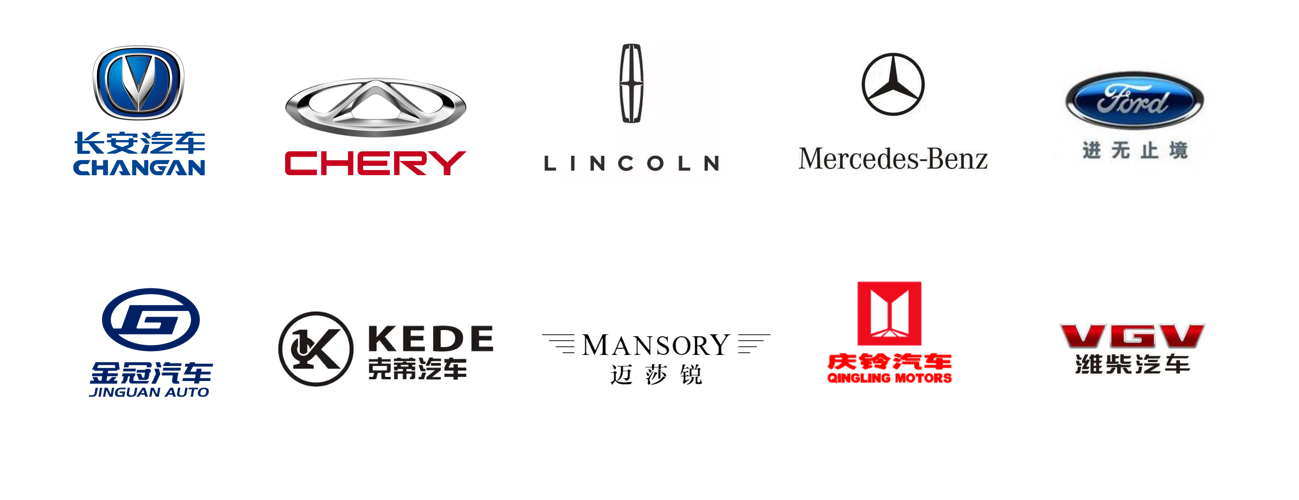
Voorbeeldvertoning
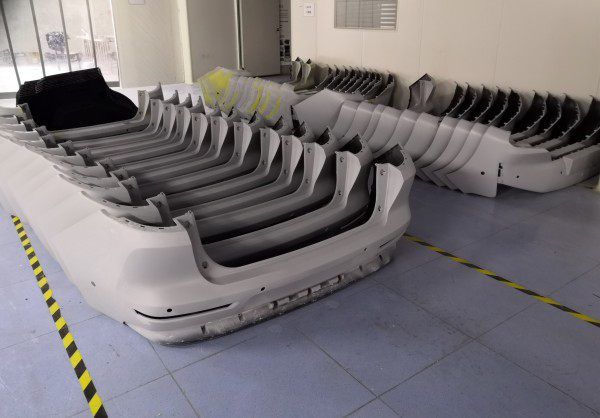
Motorvoertuigbuffer
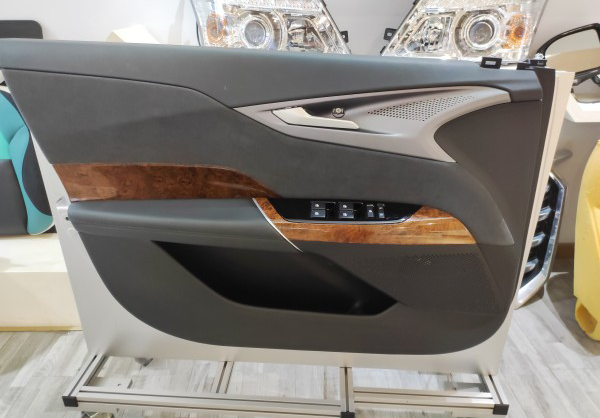
Motordeurpaneel
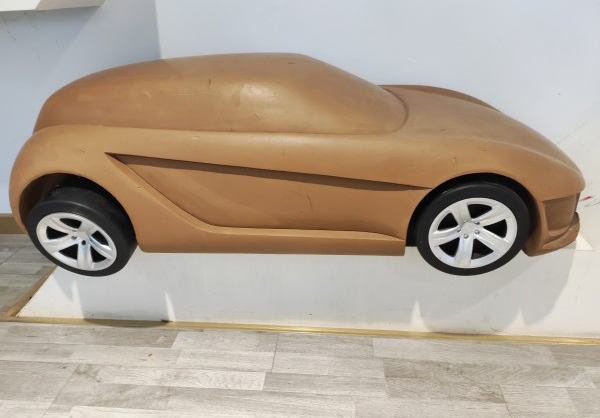
Motorvorm
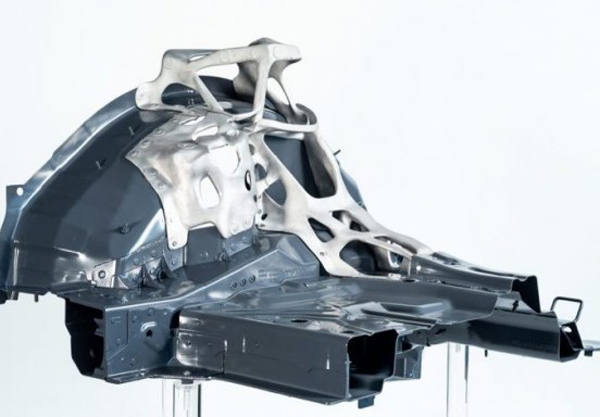
Spatbordbalk
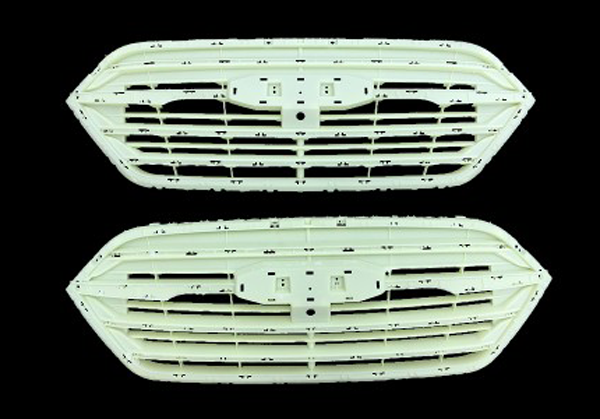
Rooster
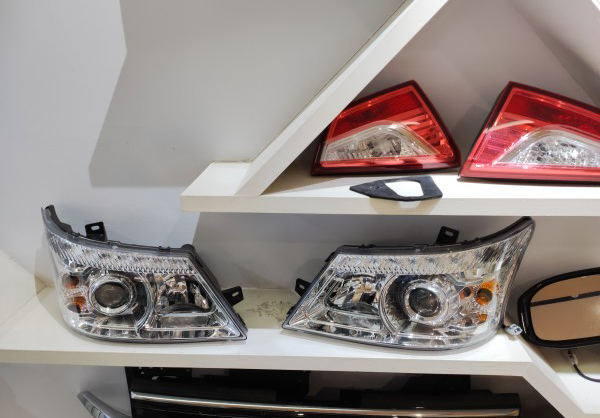
Koplamp
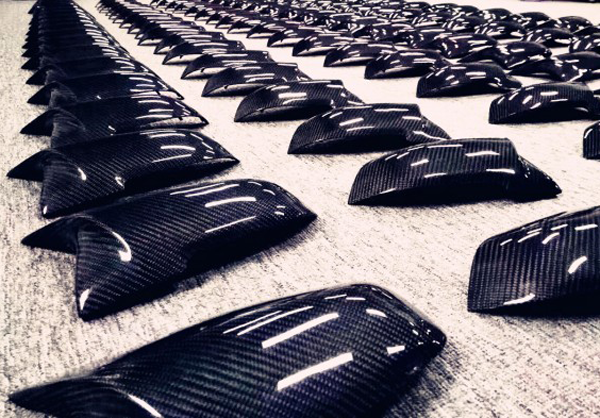
Wippaneel
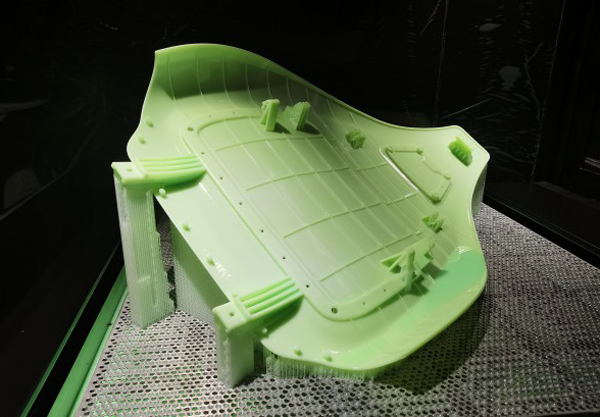
Saet Deel
Itemproses
1. Vereistes: Verskaf die algehele wysigingsontwerpskema en die prototipe-ontwerp van die gewysigde onderdele, modelleringsstruktuurontwerp, ens.

2. Monster: Produseer vinnig monsters deur 3D-drukwerk vir ontwerpverifikasie, monteringsverifikasie, uitstallingsvertoning en meer

3. Klein bondel: Deur 3D-drukwerk en silikoonvormproefproduksie van 5-200 produkte, toetsmarkterugvoer

4. Inspuitvorm: Die gebruik van eenvoudige inspuitvormmassaproduksie van 200-1000 gewysigde onderdele, wat 30% -70% bespaar op vormkoste